Analysis of the Core Advantages of the Hybrid Solution Combining Dry Coolers and Closed-Circuit Cooling Towers
- Model
- BY-V-GLQ
Item specifics
- Core Component
- Finned Tube Heat Exchangers
- Tube Diameter
- 7mm, 9.52mm, 12.7mm, 15.88mm
- Casing Material
- Galvanized Steel, Aluminium, Stainless Steel
- Tube Material
- copper, stainless steel
- Fin Material
- aluminum, copper, stainless steel
Review
Description
Background:
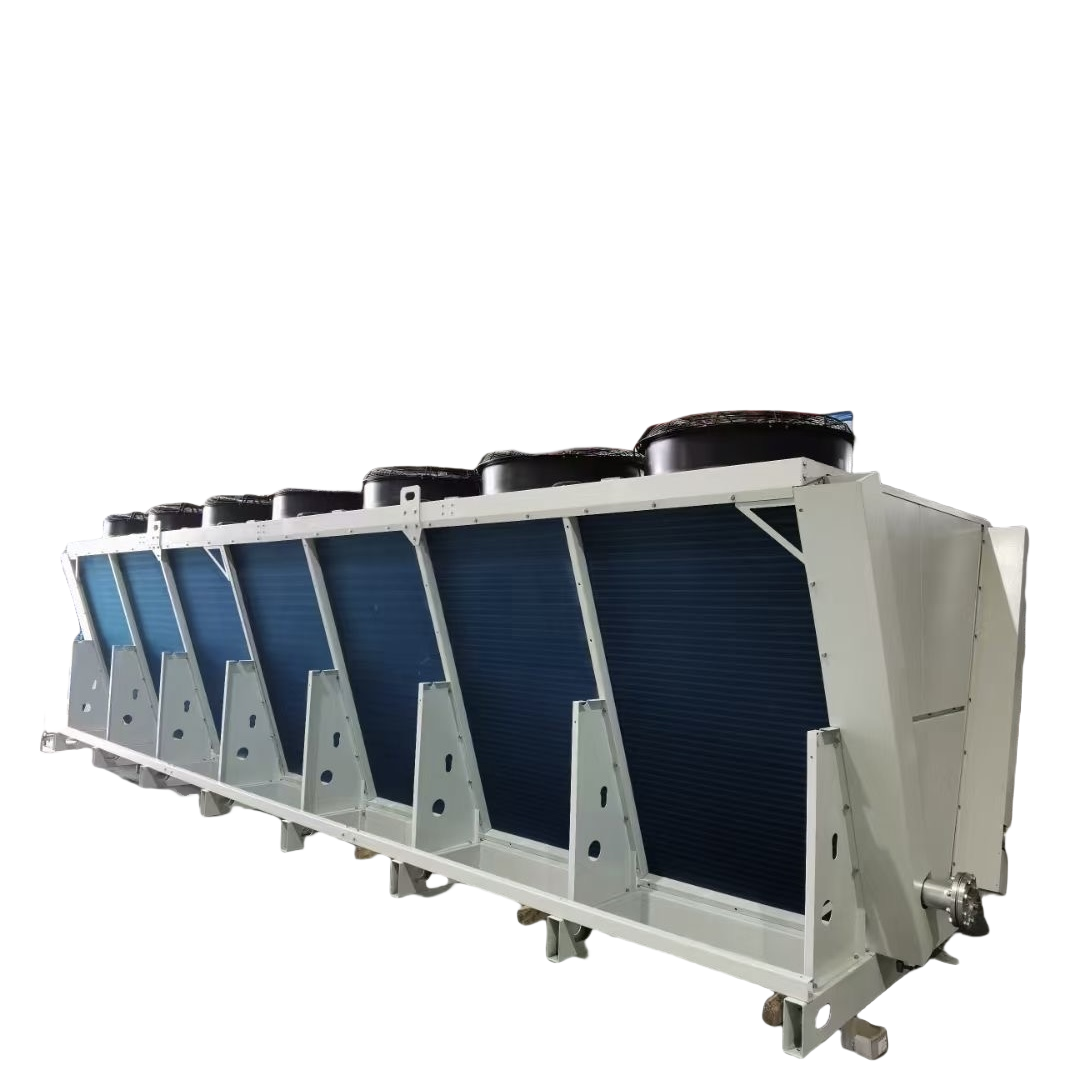
In high-energy-consumption server scenarios such as mining farms and AI liquid-cooled data centers, the efficiency and stability of cooling systems directly impact equipment operational safety and operating costs. Although traditional closed-circuit cooling towers and open-circuit cooling towers are widely used, their issues of high water consumption, susceptibility to scaling, and complex maintenance are becoming increasingly prominent. To address these challenges, we have conducted extensive theoretical and practical research and developed a hybrid solution combining dry coolers with closed-circuit cooling towers. Below, we will analyze its core advantages in detail, covering multiple dimensions such as water-saving efficiency, heat dissipation performance, economic benefits, environmental adaptability, and system flexibility. By integrating engineering practices with thermodynamic principles, we demonstrate its comprehensive value in cooling applications for mining operations.
Water-saving efficiency: Breaking through the water resource bottleneck
1. The water-saving logic of staged cooling: The hybrid solution adopts a tiered strategy of "pre-cooling with dry coolers + deep cooling with closed-circuit cooling towers" to maximize the advantages of both cooling methods:
1.1 Dry cooler: Using air as the sole cooling medium, with zero water consumption, it handles 60%-70% of the basic heat dissipation load, precooling the circulating medium (e.g., glycol solution) from a high temperature (e.g., 45°C) to a moderate temperature (35°C-38°C).
1.2 Closed-circuit cooling tower: Only needs to handle the remaining 30%-40% of the high-temperature load, and further cools the medium to the target temperature (e.g., 28°C-30°C) through spray water evaporation (indirect heat exchange).
Water-saving effect: The water consumption of a closed cooling tower is proportional to the processing load. By pre-cooling with a dry cooling tower, the evaporative water loss of the closed cooling tower can be reduced by 60%–70%. For example, for a heat dissipation demand of 1000 kW:
Traditional closed cooling tower: daily water consumption of 12-15m³ (full load evaporation).
Hybrid solution: Daily water consumption reduced to 3-5m³, achieving a water-saving rate of 75%-80%.
2. Adaptability in high-temperature and water-scarce regions: In extremely arid regions (such as deserts in the Middle East), the hybrid solution further optimizes water conservation through the following design:
2.1 Dry cooler side spray assistance: High-pressure atomizing nozzles are installed at the air inlet of the dry cooler, utilizing a small amount of water (0.5-1 m³/day) to absorb heat through evaporation, reducing the air temperature by 5-8°C and improving the dry cooler's efficiency by 20%-30%.
2.2 Closed-circuit tower circulating water reuse: The spray water from the closed-circuit tower is recycled after sedimentation and filtration to reduce the make-up water volume.
2.3 Case data: After adopting the hybrid solution at a mining site in Saudi Arabia, the average daily water consumption decreased from 18m³ (traditional closed-circuit cooling tower) to 4.2m³, while maintaining the mining rig chip temperature below 65°C.
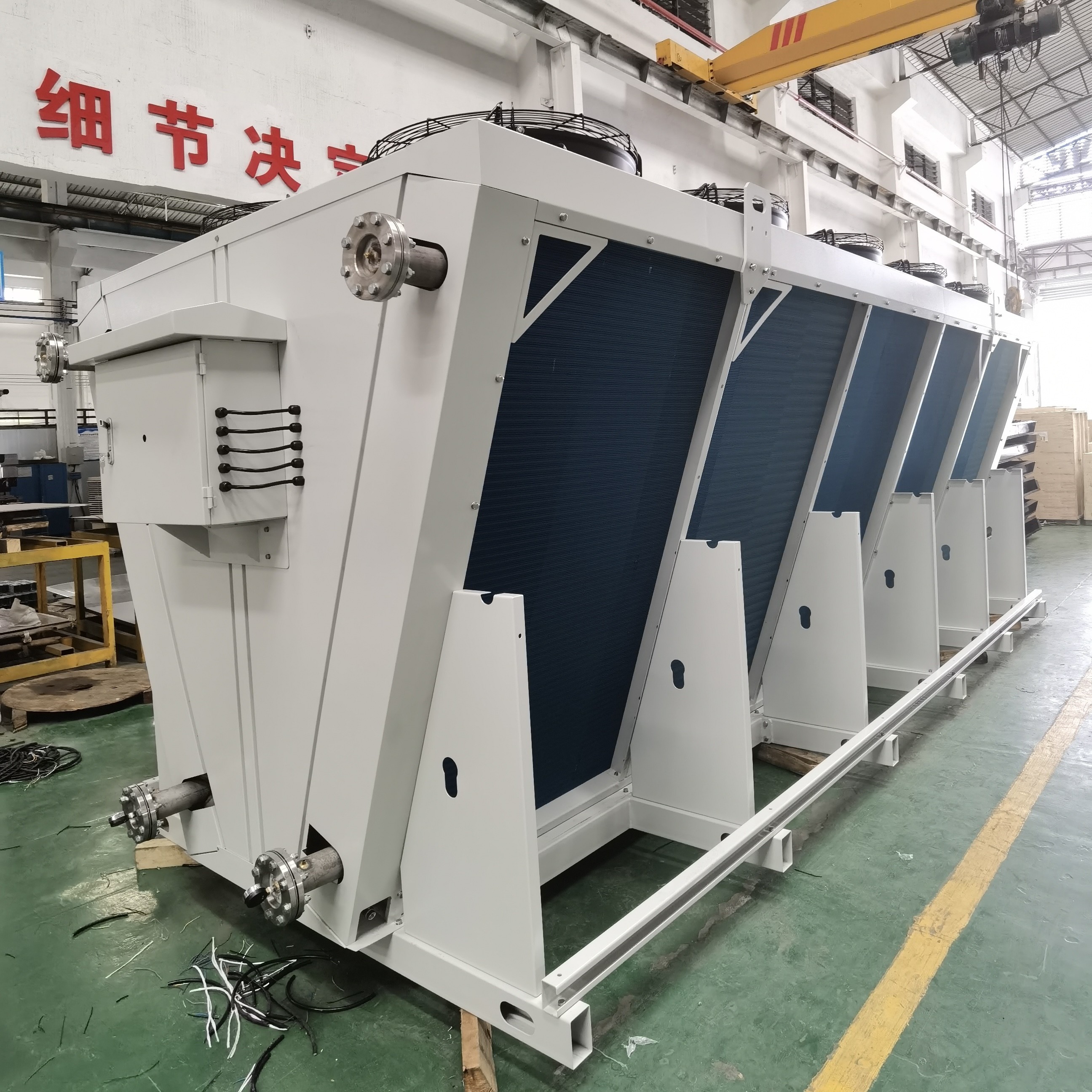
Heat dissipation efficiency: Stable output in high-temperature environments
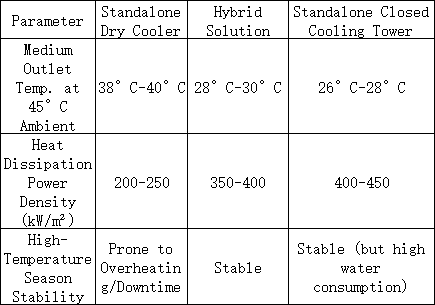
1. Thermodynamic synergistic effect:
1.1 The dry cooler precools to reduce the inlet temperature of the closed-circuit cooling tower:
Assuming the ambient temperature is 45°C, the dry cooler precools the circulating medium from 45°C to 35°C. At this point, the heat transfer temperature difference (ΔT) of the closed cooling tower increases from 10°C (traditional closed cooling tower inlet 45°C → target 35°C) to 15°C (inlet 35°C → target 20°C), resulting in a 50% improvement in heat transfer efficiency (according to the heat transfer formula Q = U * A * ΔT).
1.2 High-efficiency compensation for evaporative cooling in closed-circuit cooling towers:
The closed cooling tower, based on precooling by a dry cooler, achieves further temperature reduction through water spray evaporation (latent heat absorption). For example, at an ambient temperature of 45°C, the hybrid solution can control the medium outlet temperature to 28°C–30°C, whereas a standalone dry cooler can only achieve 38°C–40°C.
2. High-temperature resistance comparison: As shown in the figure on the left.
Conclusion: The hybrid solution can achieve 90% of the heat dissipation performance of a closed-circuit cooling tower while reducing water consumption by 75%, and it is significantly superior to an independent dry cooler.
Economy: Life-cycle cost advantage
1. The balance between initial investment and operational costs:
1.1 Initial investment: The hybrid solution requires the configuration of dry coolers, closed cooling towers, and an intelligent control system, resulting in costs that are 40%-50% higher than a single closed cooling tower (for example: a 1000kW system investment of 280,000$ vs 200,000$ for a closed cooling tower).
1.2 Long-term returns:
Water-saving costs: In regions with high water prices (e.g., the Middle East, where water cost > $5/m³), the hybrid solution can save $30,000–$50,000 in annual water expenses.
Energy-saving benefits: The dry cooler has no water pump energy consumption, and the closed cooling tower reduces fan and water pump power consumption by 30%-40% due to lower load, resulting in annual electricity cost savings of $15,000-$20,000.
Maintenance cost: Dry coolers have no scaling issues, and closed-circuit towers reduce cleaning frequency by 50% due to reduced load.
2. Calculation of Investment Payback Period (Using a Middle East Mining Site as an Example):
As shown in the figure on the right.
Conclusion: The hybrid solution can recoup the additional investment through water and electricity savings within five years, with long-term costs significantly lower than those of a closed-circuit cooling tower.
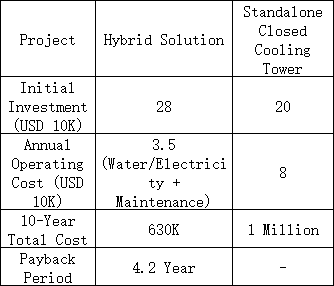
Environmental adaptability: Reliable performance in extreme conditions
1. Dynamic adaptation of temperature and humidity:
1.1 In high-temperature, low-humidity environments (e.g., deserts):
The spray system of the dry cooler fully utilizes the high evaporation potential of dry air, increasing air cooling efficiency by 30%; the closed-circuit cooling tower further reduces temperature on the basis of pre-cooling, avoiding heat dissipation bottlenecks caused by high temperatures.
1.2 In high-humidity environments (e.g., Southeast Asia):
Closed-circuit cooling towers can still dissipate heat through sensible heat exchange (without relying on evaporation). The hybrid solution intelligently allocates the load, turns off the spray system, and prioritizes the use of closed-circuit cooling towers.
2. Resistant to extreme temperature fluctuations:
2.1 Daytime high temperature: Activate the deep cooling mode of the closed cooling tower to ensure the medium temperature meets the standard.
2.2 Low temperature at night: Only operate the dry cooler and shut down the closed-circuit cooling tower to save energy and water.
2.3 Case Study: An Australian mine site adopted a hybrid solution, where the system automatically switches modes in an environment with a 25°C daily temperature variation (45°C during the day → 20°C at night), reducing average daily water consumption by 70%.
System flexibility: modularity and intelligent control
1. Modular expansion capability:
Standardized design of liquid-cooled container + cooling tower group, supporting flexible expansion according to mining machine scale: A single container (500kW) is standardly equipped with 1 dry cooler + 1 closed-circuit cooling tower. For each additional container, only one additional cooling tower module is required, reducing the marginal expansion cost by 20%.
Case Study: A mining site in Inner Mongolia was constructed in three phases, expanding from 2000 kW to 6000 kW, with only a 45% increase in cooling system costs (compared to a 100% additional investment required by traditional solutions).
2. Intelligent load distribution: Dynamic algorithm control:
Automatically adjust the load ratio between dry coolers and closed-circuit cooling towers based on real-time ambient temperature, humidity, and miner load.
For example:
When the temperature is below 30°C, the closed cooling tower shuts down, and only the dry cooler operates.
When the temperature is above 35°C, the closed cooling tower starts and operates at 40%-50% load.
Fault redundancy:
If the closed-circuit cooling tower fails, the dry cooler can temporarily handle 80% of the load (with some cooling capacity sacrificed) to ensure the mining rigs do not shut down.
Summary: The core advantages of the hybrid solution
1. Ultimate Water Saving: Water consumption is only 20%-25% of that of a closed-circuit cooling tower, making it suitable for deserts and arid mining areas.
2. Efficient Heat Dissipation: Two-stage cooling achieves a medium outlet temperature of 28°C-30°C in high-temperature environments, meeting the stringent heat dissipation requirements of mining machine chips.
3. Economic Sustainability: Costs 25%-30% lower than closed-circuit cooling towers over a 10-year cycle, with an investment payback period of less than 5 years.
4. All-Climate Adaptation: Stable operation from deserts to tropical rainforests, with intelligent adjustment to temperature/humidity fluctuations.
5. Elastic Architecture: Modular design supports rapid expansion, while intelligent control enables on-demand resource allocation.
Application scenario priority:
Preferred choice: Medium to large mining farms with ambient temperature >35°C, water resource cost >$3/m³, and miner power density >15kW/cabinet.
Recommended configuration: Pair 1-2 liquid-cooled containers with 1 set of dry cooler + closed-circuit cooling tower to balance initial investment and long-term returns.
Conclusion:
Through a hybrid solution of dry coolers and closed-circuit cooling towers, mining farms and AI liquid-cooled data centers can achieve the optimal balance between heat dissipation efficiency and resource consumption in extreme environments, providing reliable support for high-performance computing scenarios such as Bitcoin mining and data center operations.
- Specifications can be tailored to suit each application, with different materials, sizes, noises and cooling mediums available.
- contact us