Stainless Steel Tube Dry Cooler: An Innovative Cooling Solution for Mines and AI Liquid-Cooled Data Centers
- Model
- BY-V-GLQ
Item specifics
- Core Component
- Finned Tube Heat Exchangers
- Tube Diameter
- 7mm, 9.52mm, 12.7mm, 15.88mm
- Casing Material
- Galvanized Steel, Aluminium, Stainless Steel
- Tube Material
- copper, stainless steel
- Fin Material
- aluminum, copper, stainless steel
Review
Description
V-Type Dry Cooler Key Features:
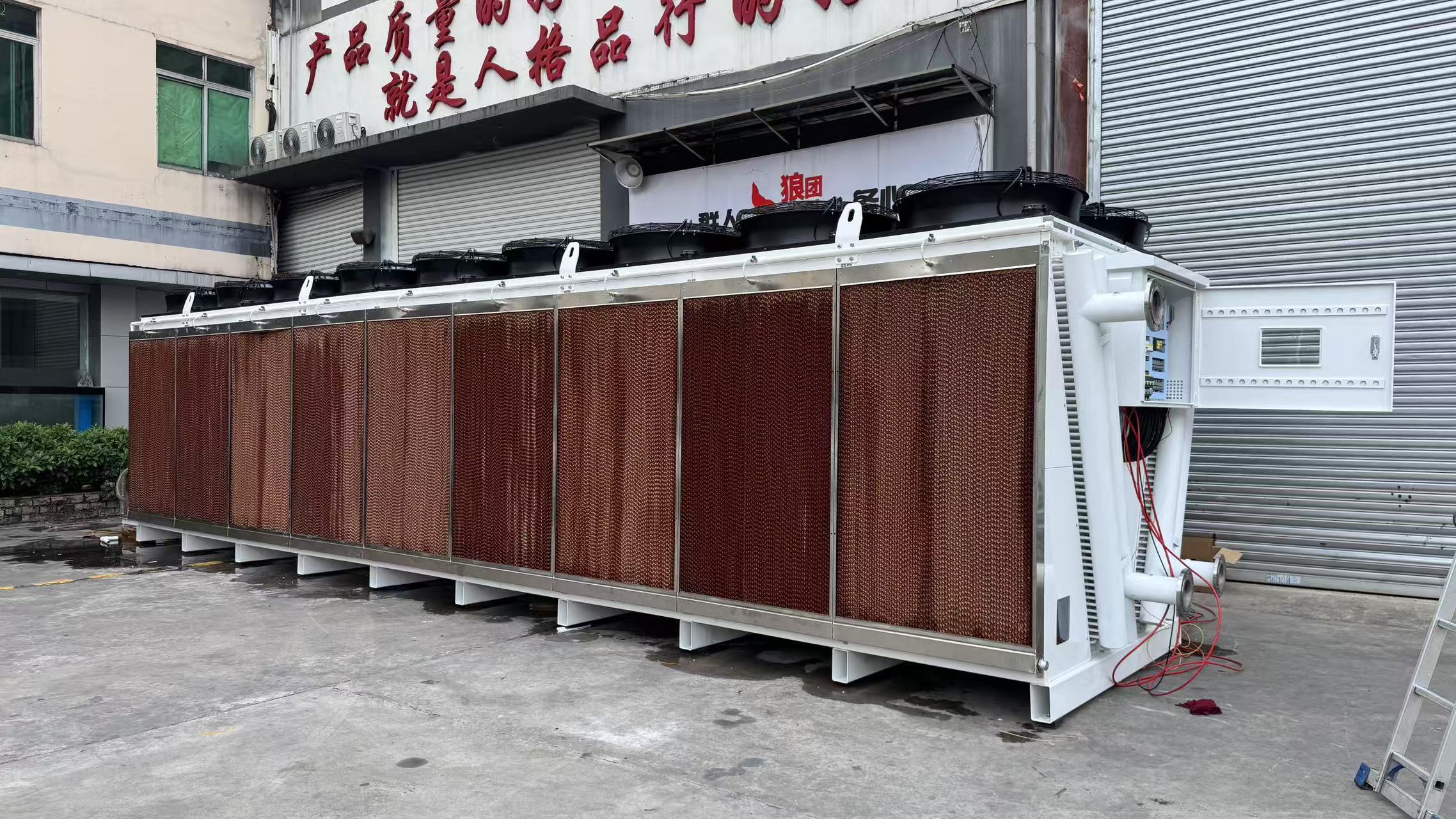
1. V-Type design for easy installation and space-saving.
2. Efficient heat dissipation to prevent equipment overheating.
3. Specifically designed for industrial cooling systems in data centers and mines.
4. Reliable and durable construction for long-lasting performance.
Background:
In high-energy-consumption server scenarios such as mining farms and AI liquid-cooled data centers, the efficiency and stability of cooling systems directly impact equipment operational safety and operating costs. Although traditional closed-circuit cooling towers and open-circuit cooling towers are widely used, their issues such as high water consumption, susceptibility to scaling, and complex maintenance are becoming increasingly apparent. In recent years, stainless steel tube dry coolers have emerged as an ideal alternative to traditional cooling towers, leveraging their flexible "dry-wet hybrid" mode, corrosion-resistant properties, and environmental adaptability. This article will provide an in-depth analysis of the advantages of this innovative cooling solution from the perspectives of technical principles, operational modes, and economic and environmental value.
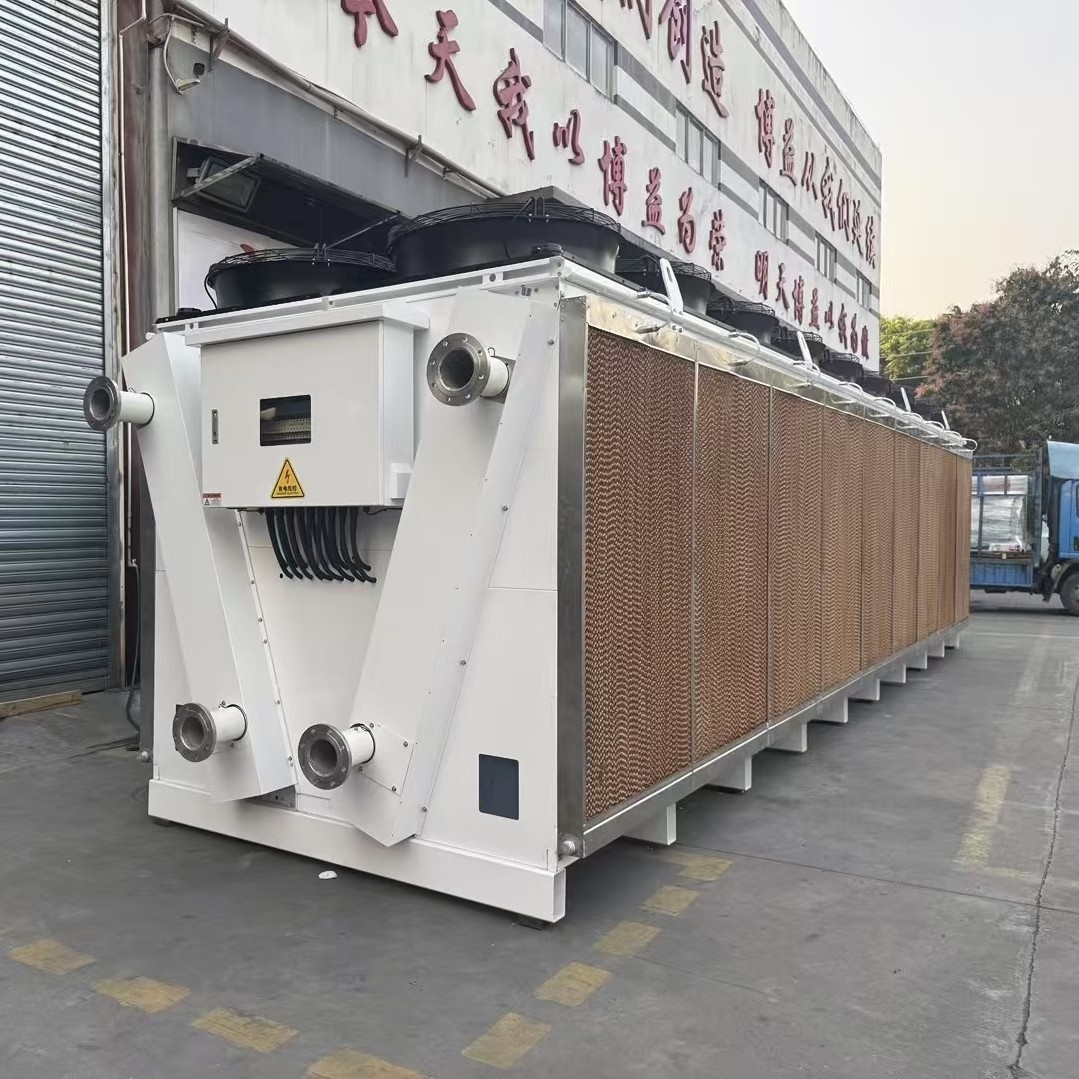
The limitations of traditional cooling towers:
1. The pain points of closed-circuit cooling towers:
Closed-circuit cooling towers rely on indirect heat exchange between circulating water and air, requiring additional water pumps and spray systems, resulting in relatively high energy consumption. The internal piping is prone to scaling or corrosion due to water quality issues, leading to increased maintenance costs.
2. The defects of open-circuit cooling towers:
Open-circuit cooling towers directly cool water through evaporation. Although they have low initial investment costs, they consume large amounts of water and pose high risks of water contamination, making them prone to bacterial growth and pipe blockages. As a result, their applicability is limited in arid regions or areas with strict environmental regulations.
The core advantages of stainless steel tube dry coolers:
1. Dry running: Balancing environmental friendliness and energy efficiency:
When the ambient temperature is suitable (e.g., 15~30°C), the stainless steel tube dry cooler can operate entirely in air-cooling mode.
1.1 Zero Water Consumption Design:
Through an efficient finned tube structure, heat is directly carried away by air convection without consuming water resources, making it particularly suitable for water-scarce regions.
1.2 Corrosion resistance and long service life:
The stainless steel material is resistant to high-salt, high-humidity, and acidic environments, avoiding the corrosion issues associated with traditional copper and carbon steel pipes, extending the service life by over 30%.
2. Wet-assisted: Elasticity Enhancement in High-Temperature Environments:
When the ambient temperature exceeds 35°C or there is a sudden increase in local heat load, the stainless steel dry cooler can enhance heat dissipation efficiency through various wet-assisted methods. The key lies in utilizing the latent heat of water evaporation (approximately 2260 kJ/kg) to achieve efficient cooling, while minimizing water consumption through intelligent control. Below is a detailed analysis of three typical humidification cooling technologies:
2.1 Air spray humidification: precise spraying and enhanced evaporation:
2.1.1 Working Principle: High-pressure atomizing nozzles are installed at the air inlet or on the surface of the finned tubes of the cooler, spraying water into fine droplets of 10~50 microns. These droplets are directly dispersed into the high-temperature airflow or onto the heat sink surface. The water mist rapidly evaporates, absorbing a significant amount of heat and notably reducing the air temperature (achieving a 5~15°C temperature drop). Meanwhile, it enhances the heat exchange temperature difference between the air and the stainless steel finned tubes.
2.1.2 Technical Advantage: Dynamic Adjustment - Real-time monitoring of environmental parameters via temperature and humidity sensors, with AI algorithms automatically regulating spray frequency and water volume. For example, the system activates spraying when relative humidity falls below 40% and switches to pure dry operation when humidity exceeds 60%, preventing ineffective humidification.
2.1.3 Water-saving design: A closed-loop water circulation system is adopted to collect unevaporated condensate and filter it for reuse, reducing water consumption to only 10%~15% of that of traditional open-circuit cooling towers.
2.1.4 Anti-clogging optimization: The nozzle is equipped with a built-in self-cleaning filter screen and a backwashing function to prevent blockages caused by water impurities (especially suitable for high-dust environments such as mining sites).
2.2 Adiabatic cooling with wet pads: Passive cooling through continuous evaporation:
2.2.1 System configuration:
Install porous cellulose or fiberglass wet curtains (100-200mm thick) on the air intake side of the dry cooler. A circulating water pump evenly distributes water to the top of the wet curtains, forming a downward-flowing water film. When external high-temperature air passes through the wet curtains, the water film evaporates and absorbs heat, cooling the air before it enters the finned-tube heat exchangers of the dry cooler.
2.2.2 Performance characteristics:
A. Stable Cooling: Wet curtains can reduce the inlet air temperature to near the wet-bulb temperature (for example, when the dry-bulb temperature is 40°C and humidity is 30%, the outlet air temperature of the wet curtain can drop to 28°C), providing a low-temperature air source for subsequent dry coolers.
B. Low-energy operation: The wet curtain system only requires a small water pump to operate, consuming over 50% less energy compared to traditional cooling tower fans.
C. Anti-pollution design: The wet curtain surface is coated with an antibacterial layer, combined with an automatic drain valve, to prevent algae growth and scale deposition.
2.3 Finned humidification cooling: Direct surface evaporation for enhanced heat transfer:
2.3.1 Innovative structure: Cover the stainless steel fin surface with a hydrophilic coating or microporous ceramic layer to evenly distribute water across the entire fin surface through capillary action. When high-temperature airflow passes through, the water film on the fin surface evaporates, directly carrying away heat from the fins while simultaneously lowering the air temperature.
2.3.2 Technical breakthrough:
A. The enhancement of heat transfer coefficient: Evaporative cooling can increase the local heat transfer coefficient of fins by 30%~50%, making it particularly suitable for high heat flux scenarios such as GPU/ASIC chip heat dissipation.
B. Anti-corrosion protection: The hydrophilic coating combined with stainless steel substrate avoids the risk of oxidation when traditional aluminum fins encounter water.
C. Water self-adaptation: The water supply flow is adjusted based on humidity feedback to ensure only a thin layer of water film is maintained on the fin surface, preventing excessive water residue.
2.4 The intelligent control strategy for wet assist mode:
To achieve seamless switching between dry and wet modes and optimal energy efficiency, the system integrates the following intelligent control modules:
2.4.1 Environmental perception layer: Deploy dry bulb/wet bulb temperature sensors, anemometers, and hygrometers to collect real-time environmental data.
2.4.2 Decision algorithm layer: Based on machine learning models to predict cooling demand, it automatically selects among "pure dry," "spray-assisted," or "wet curtain + fin synergy" modes.
2.4.3 Execution control layer: Adjust parameters such as the opening degree of the spray solenoid valve, the frequency of the wet curtain water pump, and the water supply pressure of the finned tubes. In the event of sudden thermal load (e.g., a surge in AI training tasks), activate the "Wet Overclocking Mode" to temporarily increase heat dissipation capacity by over 40%.
3. Structural optimization and spatial adaptability:
3.1 Compact modular design: The stainless steel tube dry cooler reduces its volume by 20%~40% compared to traditional cooling towers, enabling flexible deployment in confined mine spaces or on data center rooftops.
3.2 Low-noise operation: No high-frequency noise from fans, meeting the requirements for a quiet environment in data centers.
Case study: The transformation effect of a Bitcoin mining farm
1. Background:
In a mining site in Inner Mongolia, the summer ambient temperature reaches 42°C. The original open-circuit cooling tower caused frequent overheating shutdowns of mining machines due to scale blockage.
2. Transformation plan:
Adopt a hybrid system combining stainless steel dry coolers, adiabatic wet pads, and fin humidification, with mine recycled reclaimed water used for supplying water to the wet pads and fins.
3. Results:
Peak cooling capacity in summer increased by 55%, while miner failure rate dropped by 90%. Annual water savings reached 32,000 tons, and combined with electricity cost savings, the investment payback period was only 2 or 3 years.
Application Scenarios and Economic Benefit Analysis:
1. Mining site scenario: Reliable heat dissipation in harsh environments:
Mining sites are mostly located in remote areas with hard water quality and heavy wind-blown sand, where traditional cooling towers are prone to clogging and failure. The corrosion resistance and dry operation mode of stainless steel dry coolers can reduce maintenance frequency by 80% while eliminating downtime risks caused by water quality issues.
2. AI Data Center: Green PUE Optimization:
The heat dissipation density of AI computing clusters can reach up to 20KW per cabinet, while traditional cooling towers' high water consumption and low energy efficiency drive up the PUE (Power Usage Effectiveness). By adopting a hybrid dry-wet cooling system, the annual average PUE of data centers can be reduced to below 1.2, with water savings exceeding 70%, aligning with the requirements of the "dual-carbon" policy.
3. Life cycle cost advantage:
Although the initial investment in stainless steel dry coolers is 10%~15% higher than traditional solutions, their water and energy savings, along with low maintenance requirements, allow the cost difference to be recovered within 3~5 years. In the long term, the overall operational costs are reduced by 30%~50%.
Future Trends: Intelligentization and Multi-energy Coupling
1. With the integration of AI and IoT technologies, the new generation of stainless steel dry cooler is advancing toward intelligent regulation and multi-energy coupling.
2. Digital Twin and Predictive Maintenance: By monitoring the radiator status in real time, it predicts scaling or performance degradation, enabling proactive optimization of maintenance schedules.
3. Waste heat recovery and utilization: The hot air from the radiator outlet is used for district heating or to drive an absorption chiller, achieving cascaded energy utilization.
Conclusion:
The stainless steel tube dry cooler, through its flexible "dry-wet hybrid" design and the synergy of three auxiliary wet technologies—air spray, adiabatic wet pads, and fin humidification—not only overcomes the efficiency limitations of pure dry cooling in high-temperature environments but also redefines the environmental adaptability of cooling systems with "precision water usage" and "intelligent regulation." For AI data centers and mining farm servers, this hybrid cooling architecture, based on dry cooling with wet assistance, represents the optimal solution to address the dual challenges of extreme climates and energy-saving carbon reduction. It strikes the best balance between resource conservation, environmental adaptability, and operational costs. For mining farms and AI liquid-cooled data centers, this is not just an upgrade in cooling technology but a critical step toward sustainable development. In the future, with advancements in materials science and intelligent control technology, this solution is expected to become the standard configuration for cooling systems in high-energy-consumption industries.
- Specifications can be tailored to suit each application, with different materials, sizes, noises and cooling mediums available.
- contact us