Custom Surface Cooler for Flue Gas Recovery
- Model
- BY-BLQ
Item specifics
- Core Component
- Finned tube heat exchangers
- Tube Diameter
- 7mm, 9.52mm, 12.7mm, 15.88mm
- Casing Material
- Galvanized Steel, Aluminium, Stainless Steel
- Tube Material
- copper, stainless steel
- Fin Material
- aluminum, copper, stainless steel
Review
Description
Custom Surface Cooler for Flue Gas Recovery
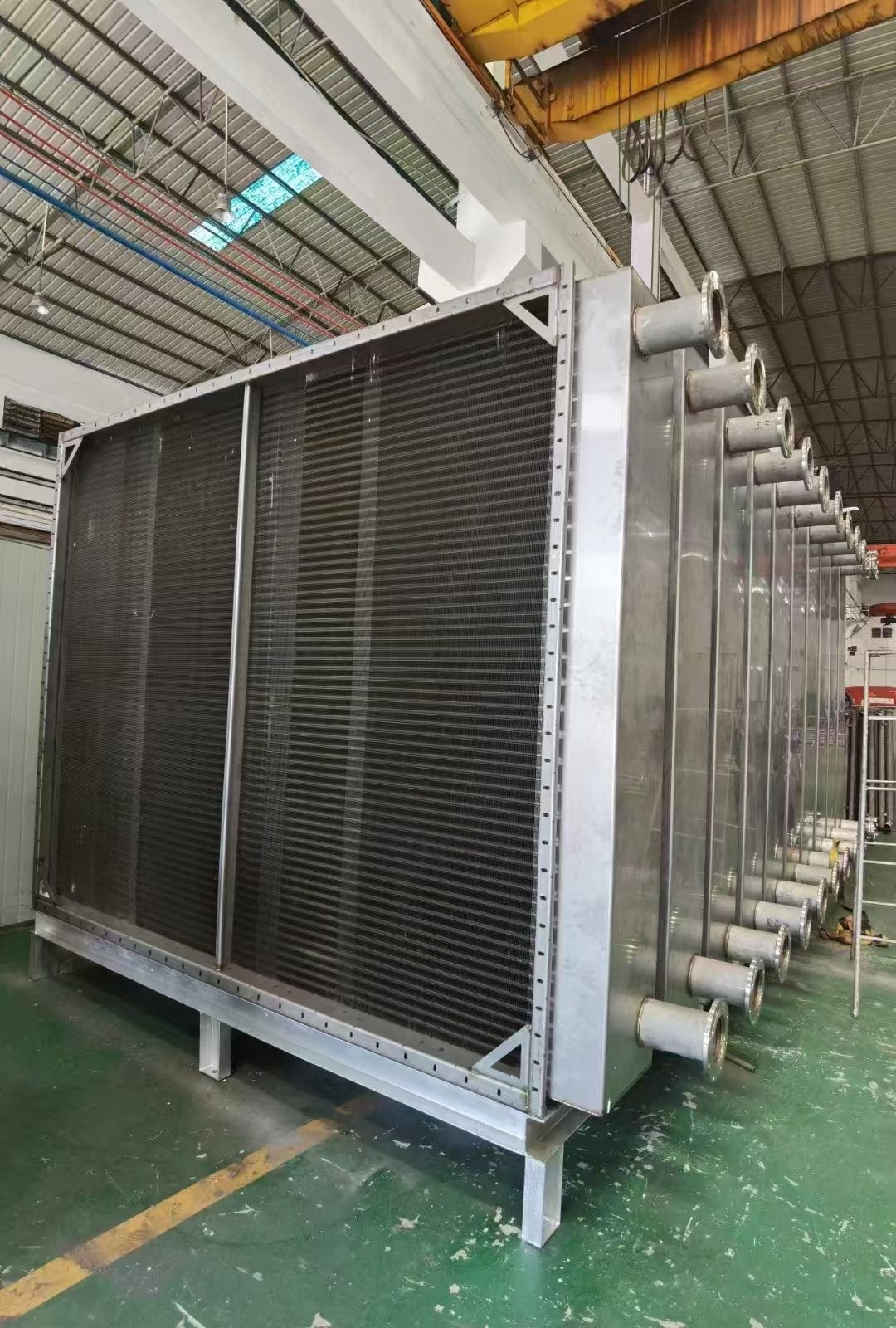
Flue gas recovery surface cooler is a kind of energy-saving and environmental protection equipment used to recover the waste heat or useful components in the flue gas discharged from the industry, which is usually applied in chemical industry, metallurgy, electric power, building materials and other industries.
Working Principle
1. Heat Recovery: High temperature flue gas passes through the heat exchanger tube bundle of the surface cooler and exchanges heat with the cooling medium inside the tube (water, air or other work materials), the temperature of the flue gas is lowered, and the cooling medium absorbs the heat and then is utilized (e.g., for heating, power generation or process heating).
2. Substance recovery: In some processes, the condensate in the flue gas may contain recoverable chemicals (e.g., acidic solutions, solvents, etc.), which are separated by condensation to achieve resourcefulness.
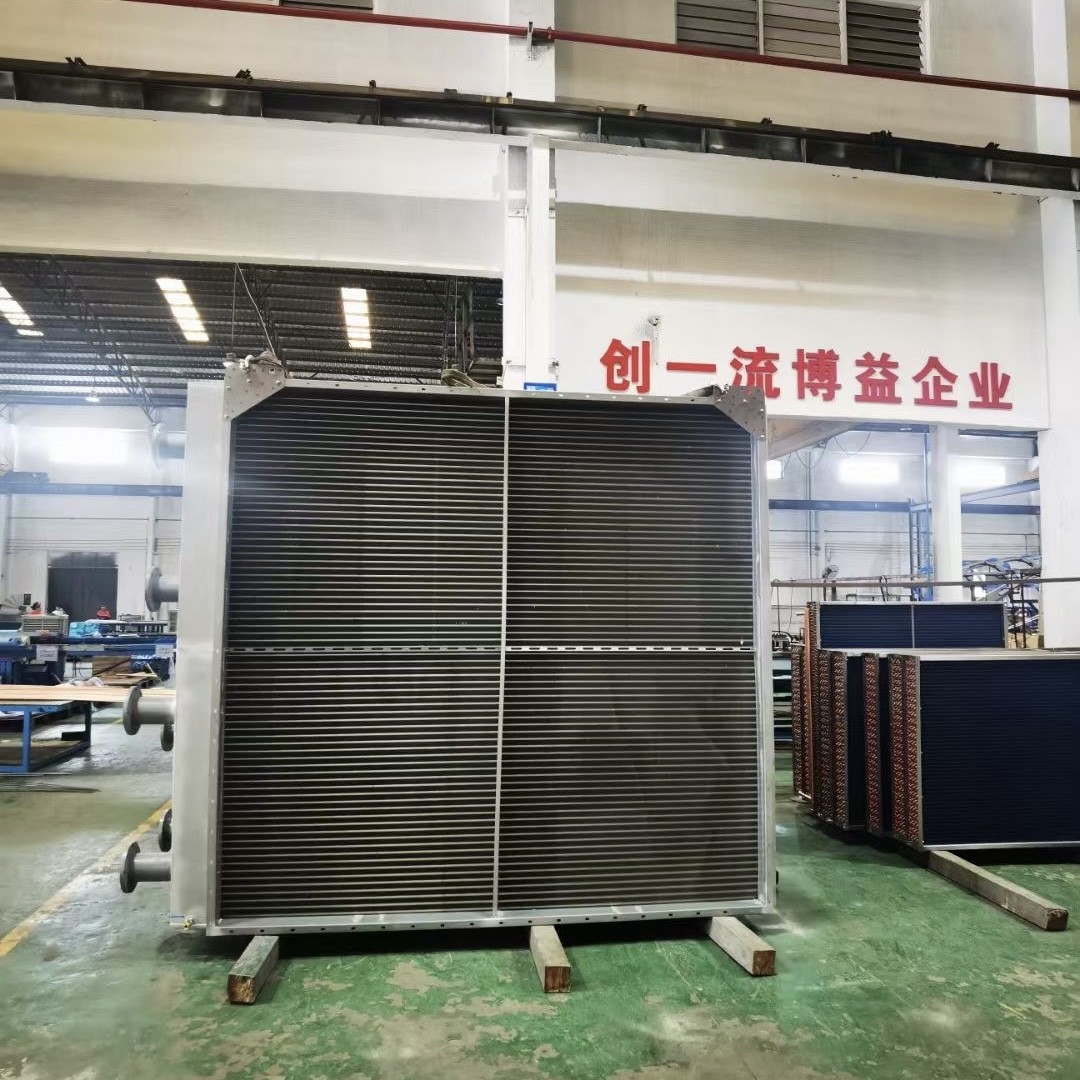
Core Structure
1. Heat exchanger tube bundle: usually made of corrosion-resistant materials (stainless steel, enameled tubes, fluoroplastics, etc.), adapted to high temperature or corrosive flue gas.
2. Condensation system: including condensate collection tank, separation device, etc., for the recovery of liquid components.
3. Ash cleaning device: for dusty flue gas, equipped with mechanical vibration, blowing or online cleaning system to prevent the accumulation of ash affecting the efficiency of heat exchange.
4. Fans/pumps: drive the flow of flue gases and cooling medium.
Key Performance Parameters
1. Heat transfer efficiency: depends on temperature difference, flow rate, heat transfer coefficient (usually designed for 60%~85%).
2. Resistance loss: need to balance the recovery efficiency and system energy consumption (generally controlled at 500~1500Pa).
3. Corrosion resistance: For flue gas containing sulfur, chlorine and other corrosive components, special materials or coatings are required.
4. Condensation rate: For substance recovery, the surface temperature needs to be optimized to achieve condensation of the target component.
Application Scenarios
1. Iron and steel/metallurgy industry: Recovery of flue gas waste heat from blast furnaces and converters.
2. Chemical industry: condensation recovery of VOCs (volatile organic compounds) or acid gases (e.g. HCl, SO₂).
3. Power industry: Utilization of flue gas waste heat from coal-fired boilers to reduce the temperature of exhaust smoke.
4. Building materials industry: heat recovery from the tail gas of cement kilns.
Design Selection Points
1. Flue gas characteristics: temperature, composition, dust content, corrosiveness, etc.
2. Recovery goals: whether heat recovery or material recovery is the main focus.
3. Space constraints: modular design adapts to site layout.
4. Ease of maintenance: Consider ash removal and access for maintenance.
Frequently Asked Questions and Solutions
1. Corrosion and clogging: Select corrosion-resistant materials, regular chemical cleaning or mechanical ash removal.
2. Decline in efficiency: monitor the heat transfer coefficient, clean up accumulated dust or replace broken parts in a timely manner.
3. Condensate treatment: supporting neutralization, filtration or evaporation and crystallization equipment to avoid secondary pollution.
Energy Efficiency Benefits
1. Direct benefit: The recovered heat can replace part of the steam or electricity consumption.
2. Environmental benefits: Reducing the exhaust temperature reduces the phenomenon of white smoke, and condensing pollutants meet the emission standards.
3. Return on Investment: Typically pays for itself in 1 to 3 years (depending on flue gas conditions and energy prices).
- Specifications can be tailored to suit each application, with different materials, sizes, noises and cooling mediums available.
- contact us